When choosing a custom office furniture manufacturer, it is crucial to evaluate whether it has high-quality production and design capabilities. High-quality office furniture can not only improve employees' work efficiency, but also enhance the professional image of the company. Therefore, knowing how to judge the capabilities of a custom furniture manufacturer will help you make an informed decision. The following points can be used as a reference for evaluation.
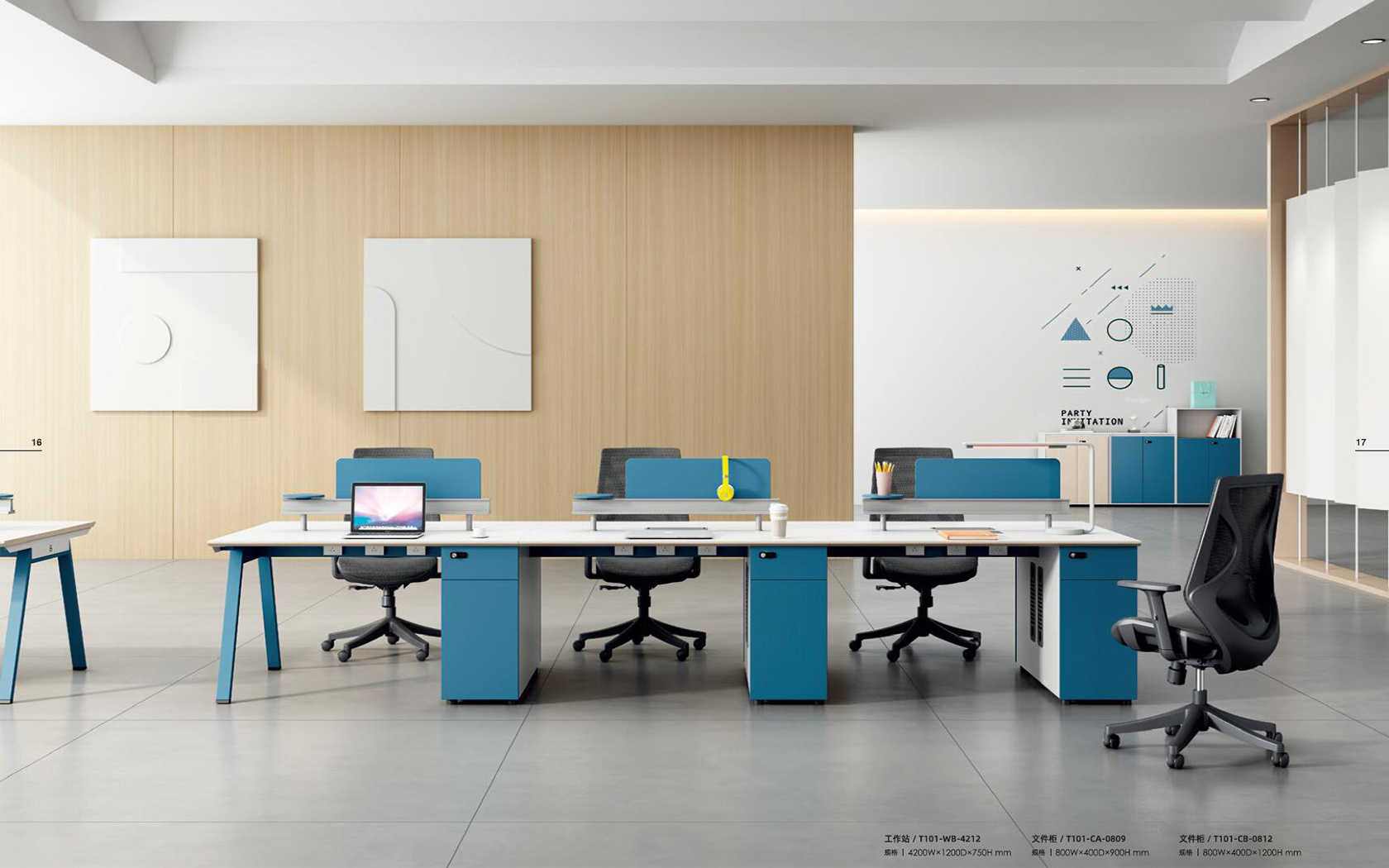
1.Manufacturer’s qualifications and certifications
importance:
Certification and qualifications are intuitive indicators to evaluate a manufacturer's capabilities, reflecting its production standards and product quality.
How to tell:
Industry certification: Look for international certifications such as ISO9001 and ISO14001 to ensure manufacturers’ capabilities in quality management and environmental management.
Patented technology: Check whether the manufacturer has patents related to office furniture design, which reflects its innovation ability.
2. Production equipment and technical capabilities
importance:
Modern production equipment and advanced technology directly affect the accuracy and quality of products.
How to tell:
Equipment modernization: Visit the factory to observe whether its equipment is modern and automated.
Technical level: Understand the manufacturer's technical processes in material handling, cutting, assembly, etc.
3. Design ability and team quality
importance:
Excellent design capabilities can meet the personalized needs of different companies and improve the overall aesthetics of the office environment.
How to tell:
Professionalism of the design team: Ask about the background and experience of the design team to see if there is a professional team of designers.
Design Cases: Check out the manufacturer’s past success stories to evaluate their design style and innovation.
4. Product quality and service life
importance:
High-quality products reduce maintenance and replacement costs and increase long-term return on investment.
How to tell:
Material selection: Ask the manufacturer about the types and sources of materials used to ensure their durability and environmental friendliness.
Quality Assurance: Understand the warranty policy provided by the manufacturer, including the warranty period and after-sales service scope.
5.Customer evaluation and word-of-mouth
importance:
Real customer reviews can provide direct feedback on a manufacturer's service and product quality, helping to judge its reliability.
How to tell:
Customer case: Ask the manufacturer if it can provide the contact information of other customers for reference.
Online reviews: Check customer reviews on third-party review platforms and social media to assess the manufacturer’s reputation in the market.
6.Customization capabilities and flexibility
importance:
The customization ability of office furniture determines whether the manufacturer can meet the specific needs and personalized requirements of the enterprise.
How to tell:
Customization options: Learn about the range of customization options offered by manufacturers, including sizes, colors, materials, and more.
Project management: Ask the manufacturer whether it provides detailed project management and customer service, and whether every link from design to delivery is transparent.
Conclusion
Choosing a customized office furniture manufacturer with high-quality production and design capabilities requires inspection from multiple aspects, including qualification certification, production equipment, design capabilities, product quality, customer reputation and customization capabilities. Through comprehensive evaluation and comparison, companies can find the most suitable partner that not only creates a comfortable office environment, but also brings long-term value and benefits to employees and the company.