In the process of customized furniture procurement for hotel chains, it is crucial to choose the right supplier. Furniture is not only the embodiment of hotel functionality and aesthetics, but also a direct extension of the overall brand image. Therefore, evaluating the supplier's production efficiency and cost control capabilities is a key link to ensure the smooth progress of the procurement project. Here are some tips to help hotel chains make informed decisions.
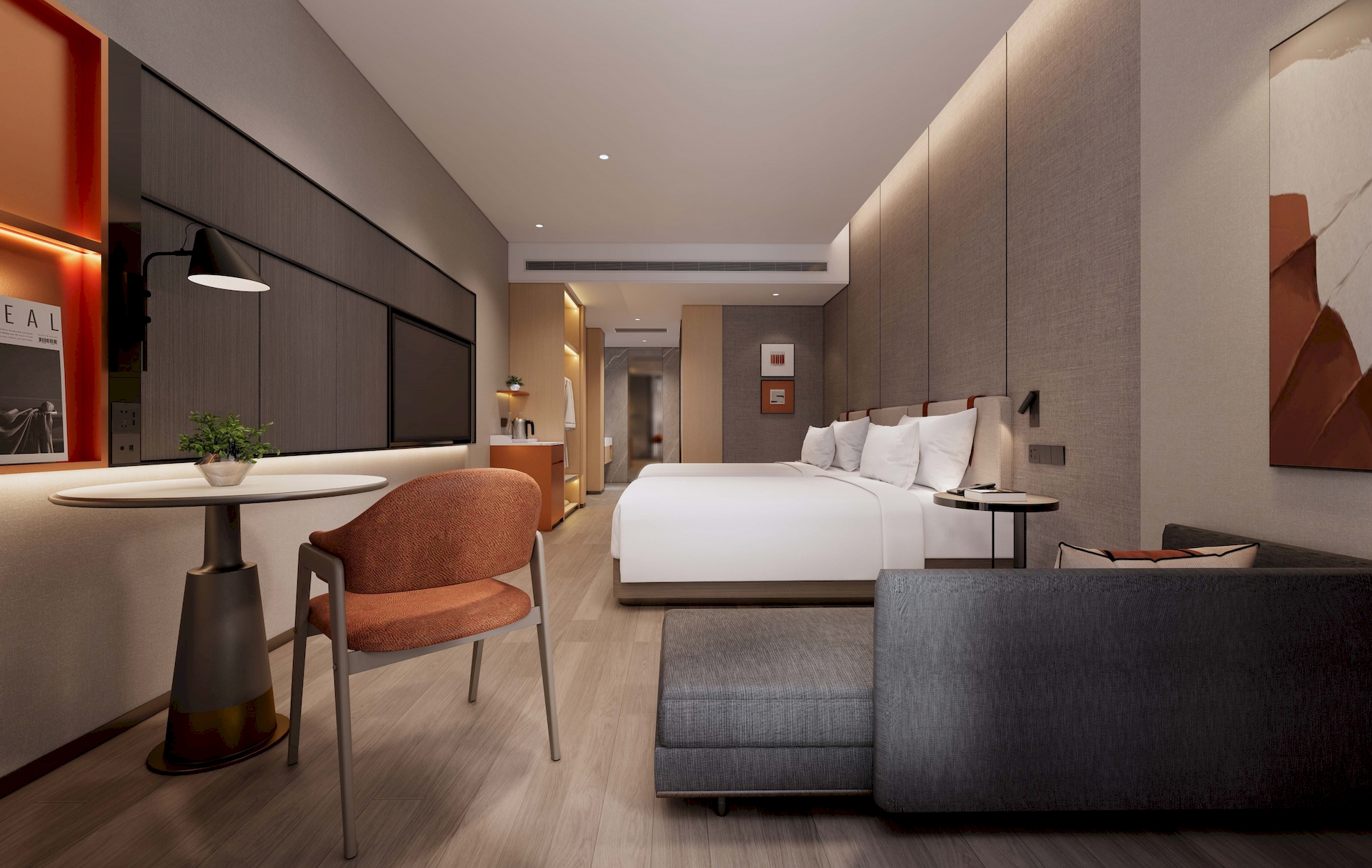
1. Production equipment and technical level
First of all, evaluating the supplier's production equipment and technical level is an important way to understand its production efficiency. Modern and automated production equipment often improves production efficiency and reduces errors caused by manual operations. Therefore, examining whether a factory adopts the latest production technology and equipment, as well as the frequency of maintenance and upgrades of these equipment, can predict its production capacity and product quality during peak periods.
2. Project management capabilities
The supplier's project management capabilities directly affect production efficiency. When evaluating, attention should be paid to whether it has a complete project management process and an experienced project team. Suppliers who can effectively schedule production, allocate resources and manage time are usually better able to ensure on-time delivery of projects. In addition, understanding its emergency handling capabilities in the face of urgent orders can also provide a basis for decision-making.
3. Transparency and traceability of production processes
An efficient supplier should have a transparent production process and a traceable record system. Transparency ensures real-time tracking of project progress, helping hotels understand every stage of production. This means problems can be identified and resolved quickly when they arise, reducing delays and increased costs. Whether suppliers use ERP systems or other digital management tools is also an important factor in considering their production efficiency.
4. Cost structure analysis
A deep understanding of a supplier's cost structure is critical to assessing its ability to control costs. This includes material costs, labor costs, production costs and other aspects. By analyzing these factors, hotels can identify where there is potential for cost savings. In addition, understanding the supplier's cost control performance and price changes in past projects can also provide a reference for judging its cost management capabilities.
5. Purchasing and inventory management
Suppliers' capabilities in raw material procurement and inventory management are also key factors affecting cost control. Suppliers with strong procurement capabilities are often able to obtain more cost-effective materials, while effective inventory management can reduce unnecessary inventory backlogs and capital tying up. Therefore, evaluating its relationships with material suppliers and inventory management strategies can help determine the supplier's cost advantages.
6. Historical performance and customer feedback
Understanding a supplier's historical performance and existing customer feedback is a powerful means of assessing its production efficiency and cost control capabilities. By communicating with other customers, hotels can gain first-hand information about their on-time deliveries, cost fluctuations, and service quality. In addition, the supplier's successful experience in similar projects can also provide a guarantee of confidence for the hotel.
7.Contract terms and risk management
Finally, a detailed review of the contract terms provided by the supplier, especially those related to costs (such as price adjustments, payment methods, etc.), can help ensure rights and control risks. At the same time, understand its risk management measures and strategies to ensure that suppliers can respond quickly in emergencies, thereby reducing the negative impact on costs and production efficiency.
in conclusion
Evaluating suppliers' production efficiency and cost control capabilities is an important step in the customized procurement of furniture for hotel chains. By in-depth examination of the supplier's production equipment, project management capabilities, cost structure and risk management strategies, hotel chains can choose the partner that best meets their needs. This not only helps ensure timely delivery and high quality of furniture, but also effectively controls costs and improves the hotel's overall operational and financial performance.